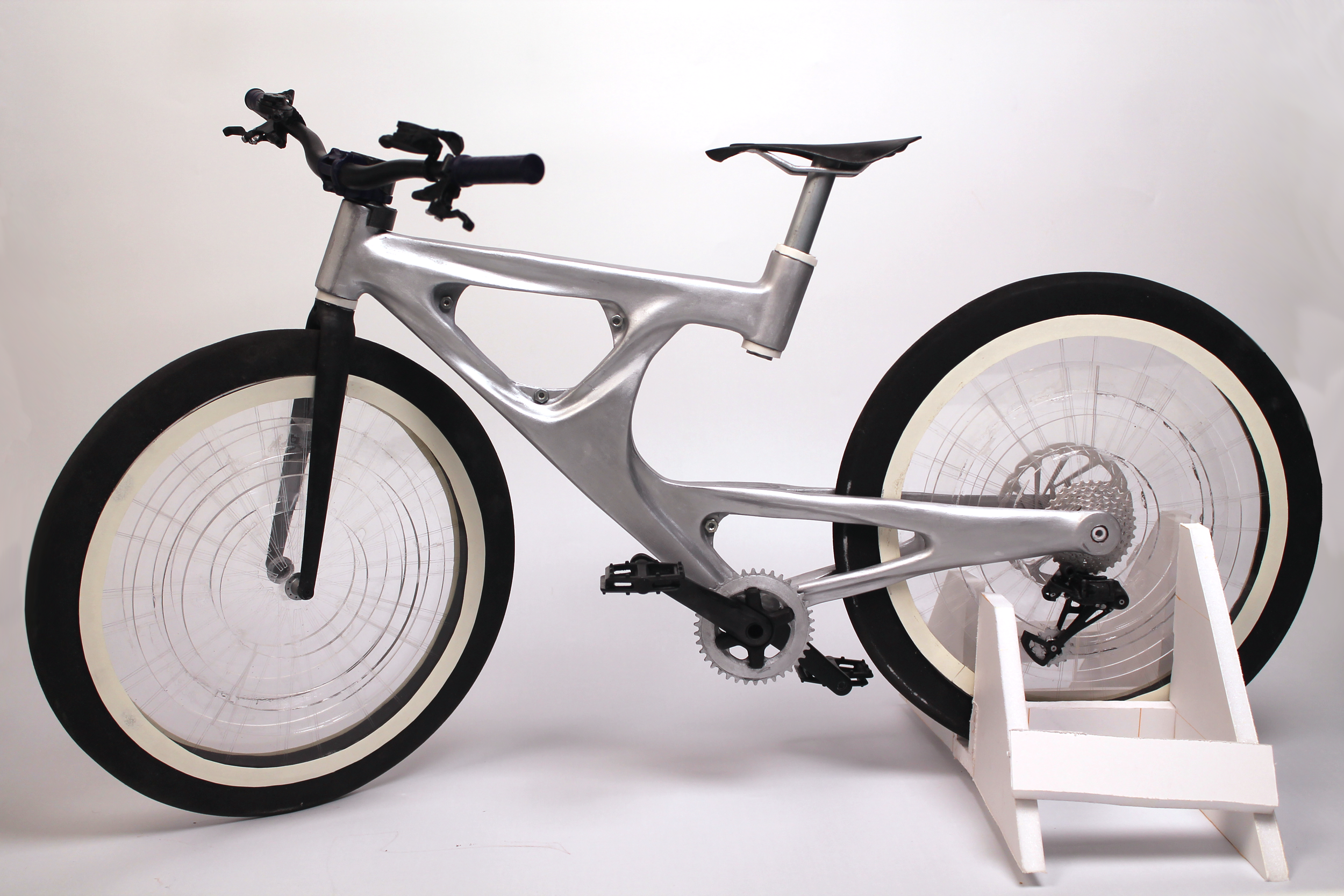
Commuter Bike
Last mile transportation has become increasingly important as our relationship with how we navigate to and from home each day. A bicycle provides the freedom of movement needed to traverse short distances easily, but there is a lack of unique and affordable bikes with an abundance of steel tube frames. Our team set out to utilize cutting edge manufacturing methods to create an economical alternative with unique aesthetic qualities that can satisfy any urban bike rider.
Project Partners
Morgan Foley
Andrew Millsap
Colin Long
Prof. Matthew Obbink
Iowa State University
Underegradate Studio
Initial Concept Development
Gathering form inspiration for the stamped super-formed autobody frames, our goal was to explore frame designs outside of conventional steel tube frames. Segmented parts and part assembly was considered at this phase. The team debated offering a mail-order business model and develop the bike to be assembled from a flat-pack, but this idea did not make it through this stage of development.
The intension for an aluminum frame with minimal use of welding is to be more economical in manufacturing. Steel is also to be used minimally in the seat tube and front fork and shocks.
Each member of the team designed their own frames and we voted to move forwards with one. My design was chosen to be developed further. As the project continued, I became responsible for overall aesthetics and manufacturing research of the frame.
Process & Research
The frame design was sculpted into the third-dimension with clay on top of 3D printed forms. A few variants where experimented with at this phase while staying true to a sleek industrial aesthetic and being considerate of manufacturing constraints.
Our final clay model was 3D scanned and translated into CAD to be refined into a working frame model. The frame was then CNC cut to become bucks for vacuum thermoforming the two halves. This would simulate the actual manufacturing process, with the aluminum being stamped and each halve being super-formed.
Main points to join the two halves would be the seat tube, front fork tube, pedal axle, and rear wheel axle. Support joints across the interior of the frame are intended to further secure the frame together.
Unfortunately, our plan did not work as intended. Our bucks for the vacuum thermoforming failed and bonded to the polystyrene. With limited time remaining, we decided to 3D print the frame.
Final Model
The raw aluminum finish is to highlight the material and manufacturing methods taken to produce this bike frame. To offer options to potential users, color variants were developed within our branding styles.
Illustration work and photography was handled by Morgan Foley. Part modeling and refining was handled by Andrew Millsap. Branding was handled by Colin Long. Final model assembly was a team effort.